中国制药装备行业经过近40年的努力取得了令人瞩目的进步,最显著的标志是药企在技改或者新建项目中,大部分装备的首选已从进口转变为国内制造的产品为主,在化药、中药、生物药领域形成了较为完整的装备行业供应链,也出现了以楚天科技、东富龙科技为代表的行业头部企业。
君实生物是一家创新药企,产品管线涵盖生物大分子、ADC、小分子创新药。近十年来,随着中国生物制药的快速发展,生物制药装备从研发走向产业化、商业化的进程取得了瞩目的进步。在新冠疫情期间,疫苗产能建设能够快速应对,正是因为制药装备企业能够完整满足工艺需求和GMP合规装备供应链。
生物反应器的分类
以君实生物主要产品所涉及的核心工艺设备生物反应器为例,可以较为清晰地看到这一核心生产装备的发展情况。
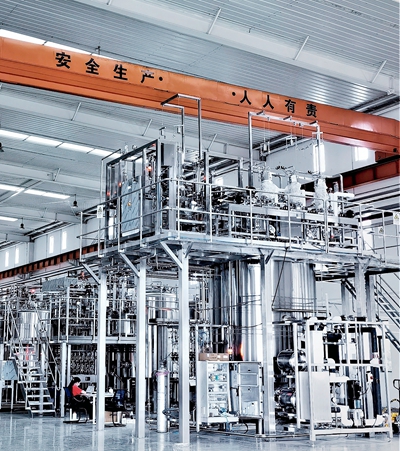
生物反应器
简单来说,生物反应器的作用,即为细胞/微生物提供生长环境并引导其产生目标产物。但由于培养的微生物/细胞十分多样化,需要实现的工艺生产目标也千差万别。例如毕赤酵母、大肠杆菌、CHO细胞、CAR-T细胞、Vero细胞,都是目前常见的生物制药培养,但它们所需要的反应器(细胞生长环境)大不相同。也就是说,生物反应器实质上是多种不同种类的生物反应器的集合。反应器发展到今天,已经形成了非常复杂的分类,而各个分支在市场的占比也各不相同,主要有以下分类:
微生物生物反应器
代表的产品包括重组疫苗、重组胰岛素及类似物衍生物、各类重组蛋白等。由于微生物的代谢生长环境容易被满足,工艺容易放大,所以通常此类反应器可以提高至相当大的工业生产规模,例如国内主要的几家胰岛素生产企业都配备了30吨规模的设备,不少生产重组蛋白的企业也具有5吨规模的设备。
贴壁哺乳动物细胞反应器
代表的产品包括灭活疫苗、细胞治疗产品等。由于哺乳动物细胞剪切敏感、生长缓慢周期长、表达率低、不易形成优势,且需要贴壁培养,其反应器设计核心需考虑尽可能降低剪切力、无菌保障,以及尽可能增加贴壁表面积等。
悬浮哺乳动物细胞生物反应器
代表为CHO细胞,由于其抗剪切能力更强、表达更加稳定、容易驯化成为悬浮培养、培养工艺更容易放大,所以目前已经成为第一大细胞培养表达平台。与此同时,不少生物技术巨头公司也开发了多种商业化细胞系,广泛地应用到各类蛋白药物产品的表达、生产,例如抗体类、融合蛋白类等。
中国生物制药起步于上世纪90年代,直至2010年,各类反应器都依赖进口,德国、瑞士、美国进口的反应器占据了大部分市场,从2010年末至2020年,国内才真正迎来了高质量反应器的本地化制造。
中国生物反应器市场的发展历程与趋势
如果以全球化的视野来看反应器市场,国内生物制药特别是抗体药物,在近十年里才从研发真正走到了商业化阶段,而欧美市场第一轮商业化产能的建设,实质上从2000年左右就开始了。罗氏/基因泰克、礼来、百时美施贵宝、默克雪莱诺等公司的第一批抗体产业化建设,很大程度上刺激了国内抗体产业的爆发,国内对大型细胞培养反应器的认识也在此之后开始深入。
为了体现这些年间的市场变化,我们把这10多年的历史分为4个阶段。
2005年—2010年:研发和早期中试阶段
在这个阶段,经过了一定时间的研发积累,以及受上市不久的抗体类产品快速增长的销售刺激,欧美巨头药企纷纷开始建设商业化生产线。此时市场需求还处于开发期,行业的细胞蛋白表达量普遍在1g/L左右或者更低,反应器普遍规模在5000L-10000L。与此同时,国内最早投入到这一轮抗体药物开发的公司已经启动,如中信国健、百泰等,都已经展开研发、中试项目。此时国内的反应器市场多以研发使用的玻璃台式反应器或者100L—500L左右的中试反应器为主,几乎都依赖进口。仅有个别国内公司开始了细胞反应器的制造,但主要以模仿贴壁细胞培养反应器为主,规模在50L左右,主要用于研发和中试,用于大分子细胞培养的生物反应器,占比不到10%。
2011年—2015年:管线抢跑阶段
紧接着前5年,欧美市场持续的研发、临床开发,特别是药品销售的快速发展,激发了各大药企及其CDMO公司商业化产线的建设规模,例如4×16000L,4×20000L,6×12000L等,并且开始建设在非欧美的产能,其中以韩国和新加坡为代表。而此阶段,国内不少药企、创新生物技术公司的管线也开始逐渐进入临床期,纷纷争抢建设早期的中试生产线及GMP生产线,以领先竞争对手完成临床试验,比较有代表性的是500L-2000L规模,也有少数公司建设了3000L和5000L规模的生产线。
在这5年中,生物反应器市场最大的份额非一次性反应器莫属,其大规模的市场推广始于2011年前后。几乎所有生物技术供应商巨头们都推出了自己的一次性反应器和液体管理系统,并且取得了显著的业绩。一次性设备具有几个显著特点:建设周期短、清洁验证简便、建设难度低、初期投资小,这些特点对于初创的生物技术公司以及前景不明的生物制药产品,很适合作为前期投资的第一条生产线,快速建立起临床产品的供应。这期间,君实生物在国内首先建成了上下游均采用一次性工艺的细胞培养生产线。到2015年,一次性生产线建成的并不多,全国建成的生产线大约为5—7家。
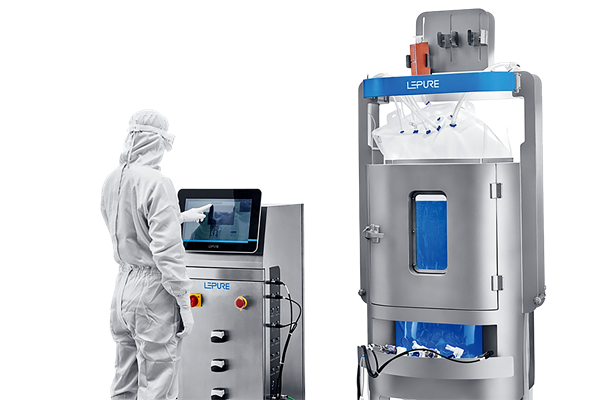
一次性生物反应器
2016年—2019年:第一批商业化生产线建设
从国际市场上来看,生物制药的产品管线仍在继续扩张,从单克隆抗体到ADC再到双抗,进入商业化阶段的药品越来越多,销售额持续火热增长。全球的市场格局极大地刺激了国内外资本涌入国内的生物制药市场,恰逢国内企业第一波产品面临进入临床三期,不少药企、生物技术公司都有了充足的资金,开始建设起自己的GMP生产线。
这个阶段的生产线大多是众多企业的第一条GMP生产线,以2000L、3000L为主,选择一次性或者不锈钢线作为第一条商业化生产线。这个规模容量下,一次性系统占比高于不锈钢系统。大部分企业仍然选择全进口设备,但已经有药企开始主动寻求本地化反应器制造商以替代进口,为未来的成本竞争做准备,有极个别的大型反应器已经在国内制造。
2020年—2021年:产能爆发、价格战、贸易战
源自前些年的行业研发投入积累、前期商业化产品的销售刺激,以及国家政策的鼓励、企业全球化的愿景、国家集采带来的成本压力等因素,生物制药企业开始建设大容量不锈钢系统商业化生产线,如3×10000L,4×10000L,4×20000L,6×12000L,8×15000L等商业化生产线项目纷纷启动建设。
在市场的进一步引导下,行业逐渐形成了共识,商业化GMP生产线,尤其是销量大的品种更适合采用不锈钢反应器,因为其能够保障更佳的工艺条件、更低的运行成本、更高程度的自动化,同时也为智能制造打好了底座。
这一阶段,外界环境也带来了本地化制造的紧迫性。中美贸易战的发生带来了警觉,美国政府已经开始限制生物技术相关产品技术的出口;生物制药行业作为国家重点鼓励发展的行业,各类政策出台,鼓励国内发展具备生产制造核心工艺设备的能力;集采带来的高度成本竞争,需相对低价的国内制造设备支持;由于疫情带来的供应链不确定性和进口耗材的成本压力,众多药企也开始考虑本地制造的一次性反应袋和反应器,不少国内公司推出相应产品。
目前,国内已经出现不少在消化进口设备工艺技术基础上的本土化制造企业,并在一些大型项目中得到了应用。国内在规划或者建设中的大型不锈钢生产线容量近200万升,其中进口品牌、进口品牌境外设计国内制造、完全国内制造的比例大约为30:20:50,国内制造占比明显上升。
生物反应器市场的未来展望
经过多年发展,在生物反应器制造领域,我国从完全进口到部分国产替代、进口品牌本地化制造,初步形成了高等级生物反应器生产线的制造能力。但和国外水平相比,在反应器设计、模块设计、自控策略、制造品质方面还有不小的提升空间,在自控单元和仪表方面还无法完全摆脱对进口产品的依赖。随着制造业数字化转型时代的来临,可以预想生物反应器技术和人工智能的融合,是数字孪生技术的发展方向。
生物反应器作为生物制药所依赖的核心工艺设备,必将随着生物制药企业的确切需求进一步发展,不光是量的增长,更应是质的增长。追求更高的细胞密度、更高的单位产量、更高度的自动化,将是药企追求的方向和目标。